Common Challenges And Solutions in Custom CNC Machining
- synergypepg
- Jul 15, 2024
- 4 min read
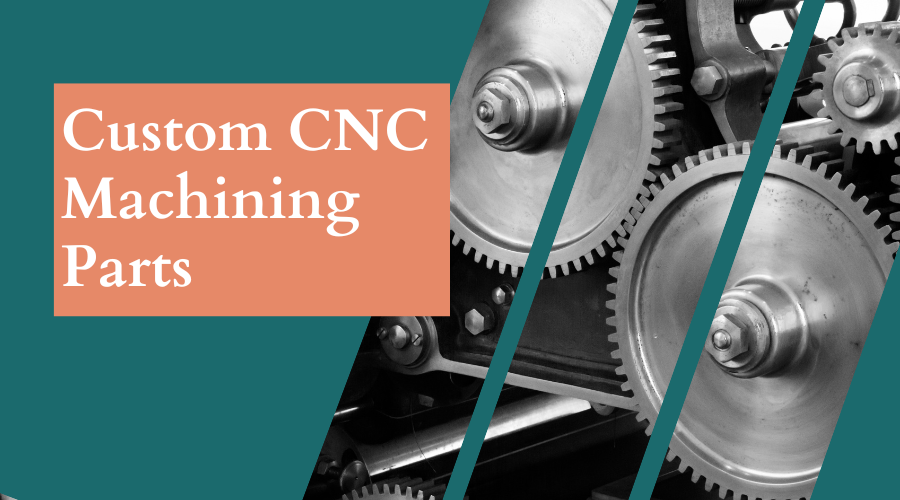
Custom CNC (Computer Numerical Control) machining is a cornerstone of modern manufacturing, offering unmatched precision, efficiency, and flexibility. From aerospace to automotive, industries rely on CNC machining to produce complex parts with exact specifications. However, like any advanced technology, Custom CNC machining parts presents its own set of challenges. Understanding and addressing these issues ensures high-quality outputs and operational efficiency. This comprehensive guide will explore the common challenges in custom CNC machining and provide actionable solutions to overcome them.
Material Selection
Challenge: Choosing a suitable material is fundamental in CNC machining. Each material has properties that affect machinability, such as hardness, strength, and thermal conductivity. Selecting an unsuitable material can lead to excessive tool wear, poor surface finish, or part failure.
Solution:
Conduct thorough research on the material properties and consult with material specialists if necessary.
Use machinability charts and resources that provide insights into how different materials behave during machining.
Consider prototyping with multiple materials for complex projects to determine the best fit for your application.
Tool Wear and Breakage
Challenge: Tool wear and breakage are common issues in CNC machining, leading to increased downtime and higher costs. These problems often arise due to inappropriate tool selection, incorrect cutting parameters, or poor material quality.
Solution:
Invest in high-quality cutting tools and ensure they are suitable for machining material.
Regularly monitor tool conditions and implement a preventive maintenance schedule to replace tools before they fail.
Optimize cutting parameters such as speed, feed rate, and depth of cut based on the specific material and tool combination.
Utilizing advanced tool coatings can also extend tool life and improve performance.
Heat Generation and Management
Challenge: Excessive heat generation during machining can lead to thermal deformation, affecting the parts' dimensional accuracy and surface integrity. Heat buildup can also accelerate tool wear and cause workpiece distortion.
Solution:
Optimize cutting speeds and feeds to minimize heat generation.
Use coolants or cutting fluids effectively to dissipate heat and lubricate the cutting area.
High-pressure coolant systems can be particularly beneficial for deep-hole drilling and high-speed machining.
Additionally, consider using materials with better thermal conductivity or implementing techniques like intermittent cutting to reduce heat accumulation.
Surface Finish and Quality Control
Challenge: Achieving the desired surface finish is critical for both the functionality and aesthetics of CNC machined parts. Inconsistent surface quality can result from tool wear, vibration, or incorrect machining parameters.
Solution:
Regular inspections of tools and workpieces should be conducted to detect issues early.
Use vibration-damping techniques, such as balancing rotating parts and securing workpieces firmly.
Adjust machining parameters based on real-time feedback to achieve the optimal speed and surface finish balance.
Automated quality control systems can also help maintain consistent quality across production runs.
Complex Geometry and Tolerances
Challenge: Custom CNC machining often involves producing parts with complex geometries and tight tolerances. Achieving high precision in intricate designs can be challenging due to machine limitations and material behavior.
Solution:
Use advanced CAD/CAM software to design and simulate the machining process before production.
This helps identify potential issues and optimize tool paths.
For extremely tight tolerances, consider multi-axis machining and fine-tuning machine calibration.
Regularly calibrate and maintain your CNC machines to ensure they operate at peak precision.
Chip Management
Challenge: Effective chip evacuation is essential to maintaining machining efficiency and preventing damage to the workpiece and tools. Poor chip management can lead to chip re-cutting, tool breakage, and surface defects.
Solution:
Use proper chip breakers and control chip size by adjusting cutting parameters.
Implement high-pressure coolant systems to aid in chip evacuation.
Design tooling and fixtures that facilitate easy chip removal and avoid chip accumulation.
For challenging materials, consider using specialized chip evacuation tools and techniques.
Programming Errors
Challenge: Programming CNC machines involves creating precise tool paths and instructions. Programming errors can lead to incorrect machining operations, resulting in part defects or machine crashes.
Solution:
Thoroughly review and test CNC programs before full-scale production.
Use simulation software to visualize and verify tool paths.
Implement standardized programming practices and provide ongoing training for CNC operators and programmers.
Regularly update software and tools to take advantage of new features and capabilities.
Machine Maintenance
Challenge: Regular maintenance is crucial for CNC machines to operate efficiently and produce high-quality parts. Neglecting maintenance can lead to machine breakdowns, reduced precision, and increased downtime.
Solution:
Establish a preventive maintenance schedule that includes routine inspections, lubrication, and part replacements.
Keep detailed maintenance records to track each machine's performance and condition.
Invest in advanced monitoring systems that provide real-time data on machine health and alert operators to potential issues.
Fixture and Work holding Design
Challenge: Proper workholding and fixture design ensure part stability during machining. Poorly designed fixtures can lead to vibration, part movement, and inaccuracies.
Solution:
Design fixtures and work-holding solutions that provide rigid and stable support for the workpiece.
Use modular and adjustable fixtures to accommodate different part geometries.
Test and refine fixture designs through simulation and prototyping.
For complex parts, consider using custom-made fixtures explicitly designed for the application.
Cost Management
Challenge: Managing the costs associated with custom CNC machining can be challenging, especially when dealing with high material expenses, tooling costs, and machine maintenance.
Solution:
Optimize material usage by implementing nesting and cutting strategies that minimize waste.
Regularly evaluate and renegotiate supplier contracts to ensure competitive pricing on materials and tools.
Implement lean manufacturing principles to reduce inefficiencies and improve productivity.
Cost-tracking software is used to monitor expenses and identify areas for cost reduction.
Conclusion
Custom CNC machining is a powerful tool in the manufacturing industry, offering unparalleled precision and versatility. However, it comes with its own set of challenges that can impact productivity and quality. By understanding these challenges and implementing practical solutions, manufacturers can optimize their CNC machining processes, reduce downtime, and consistently produce high-quality parts. Whether selecting suitable materials, managing heat generation, or ensuring proper tool maintenance, addressing these issues proactively will lead to better outcomes and a more efficient production environment.
Comments