How Material Selection Impacts Machine Parts
- synergypepg
- Nov 11, 2024
- 3 min read
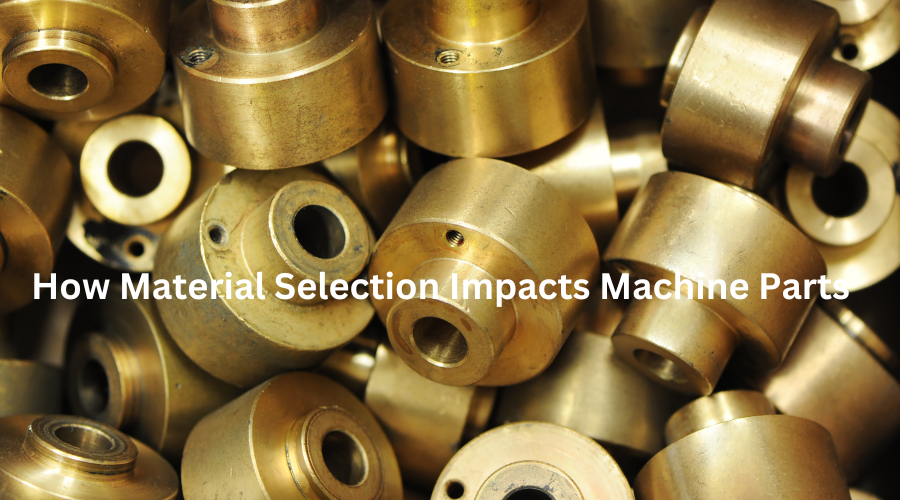
Selecting the right material is crucial to achieving quality in wholesale machining parts. Materials determine the strength, durability, and suitability of a part for its intended application. From metals to composites, each material offers unique properties that can enhance or limit a machined part’s performance. In this article, we’ll explore how material selection affects machined parts’ quality and what to consider when choosing the ideal material for your project.
1. Understanding the Importance of Material Selection in Machining
The material used in machining greatly impacts the final product's quality and performance. Choosing the right material ensures that the part will withstand the intended operational conditions, meet precision standards, and offer longevity. Inappropriate material selection can lead to premature wear, failure, or even complete malfunction of the part.
2. Key Material Properties to Consider in Machining
When choosing a material, several properties should be evaluated. These include hardness, tensile strength, ductility, and thermal stability. Each of these properties influences how the material will behave under cutting forces, heat, and stress, affecting machining efficiency and the final product's performance.
3. Metals: The Backbone of Machined Parts
Metals like steel, aluminum, and titanium are commonly used in machined parts due to their strength, durability, and versatility. Each metal has specific characteristics:
Steel is strong and wear-resistant, ideal for parts requiring high durability.
Aluminum is lightweight, corrosion-resistant, and easy to machine, making it suitable for aerospace and automotive applications.
Titanium offers excellent strength-to-weight ratio and corrosion resistance, preferred in high-stress applications like medical implants.
4. Impact of Hardness on Machining
Hardness is a crucial factor in material selection as it affects machinability. Hard materials like hardened steel and titanium alloys are challenging to machine but provide excellent wear resistance. Softer materials may be easier to machine but can wear down quickly, impacting the lifespan of the part.
5. Role of Ductility and Malleability
Ductile and malleable materials, such as aluminum and certain plastics, can deform under stress without breaking. These properties allow for greater flexibility in complex machining operations but may lead to challenges with precision, as softer materials can warp or bend more easily during machining.
6. Thermal Stability and Its Effect on Machined Parts
Thermal stability refers to a material's ability to withstand heat without altering its properties. Materials like stainless steel and high-grade alloys are known for their thermal stability, making them suitable for parts that will operate in high-temperature environments. Choosing a thermally stable material minimizes the risk of deformation and maintains part precision under heat stress.
7. Material Cost and Its Influence on Part Quality
Budget constraints are a common factor in material selection, but it’s essential to balance cost with quality. While premium materials like titanium and advanced alloys may have a higher price, their durability and performance can make them more cost-effective in the long run. Cutting costs with cheaper materials may save money upfront but could lead to increased wear, maintenance, or part failure later.
8. Corrosion Resistance for Longevity and Quality
Corrosion resistance is critical for parts exposed to moisture, chemicals, or harsh environments. Materials like stainless steel, aluminum, and special coatings can protect against rust and corrosion, extending the life of the part and reducing maintenance needs. Parts used in industries like marine, medical, and outdoor applications often prioritize corrosion-resistant materials to maintain quality over time.
9. Compatibility with Machining Processes
Certain materials are better suited for specific machining techniques. For instance, softer metals like aluminum respond well to milling, while harder metals like stainless steel require more robust processes like grinding. Choosing materials compatible with your machining methods ensures smoother operations, reduced tool wear, and higher-quality finishes.
10. Material Availability and Lead Time
Material availability is another important factor. Some materials may have long lead times due to limited supply, impacting production schedules. Choosing readily available materials can reduce wait times and costs, particularly for projects with tight deadlines. However, this decision must still account for performance requirements, as readily available materials may not always meet the necessary standards.
Conclusion
Choosing the right material for machined parts is essential for achieving high quality, durability, and performance. By evaluating factors such as hardness, ductility, thermal stability, and corrosion resistance, manufacturers can ensure their parts are not only functional but long-lasting. Remember that while material costs and availability play a role, prioritizing the right material can reduce future costs associated with maintenance and replacements. With the right material, your machined parts will deliver consistent quality and stand up to their intended applications, ensuring satisfaction for both manufacturers and end-users.
Comentarios