How Semiconductor Vacuum Chamber Parts Are Crafted and Exported
- synergypepg
- Jan 21
- 4 min read
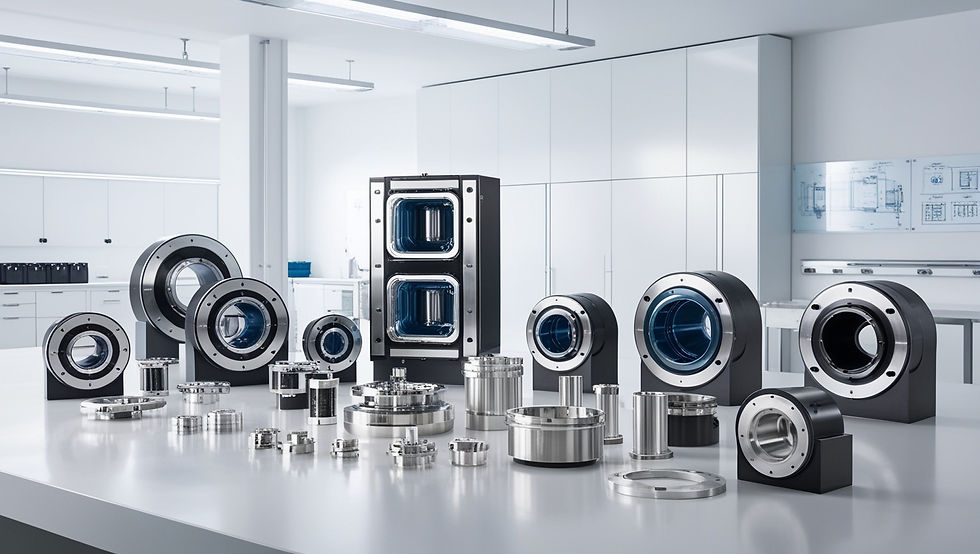
In the semiconductor industry, vacuum chambers are vital to creating the contamination-free environments required for advanced manufacturing processes such as deposition, etching, and ion implantation. Manufacturer and exporter of semiconductor vacuum chamber parts prioritize precision, quality, and compliance with international standards. This blog explores the detailed crafting process, quality control measures, certifications, challenges faced by manufacturers, and the export journey of these crucial components.
Importance of Vacuum Chamber Parts in Semiconductor Manufacturing
Vacuum chamber parts are at the core of semiconductor fabrication, enabling the processes that demand exacting precision and purity. These parts play a role in maintaining a controlled atmosphere for:
Thin-film deposition.
Plasma processing.
Wafer etching and cleaning.
Without reliable vacuum chamber components, it would be impossible to produce high-performance chips used in everything from smartphones to electric vehicles.
The Designing Phase
The design of semiconductor chamber parts begins with a thorough understanding of client requirements and industry standards. Our Engineers use CAD tools to create highly detailed designs that account for:
Precise dimensions.
High-pressure and high-temperature capabilities.
Corrosion resistance.
Integration into existing systems.
Design customization is necessary to meet the unique demands of cutting-edge semiconductor processes.
3. Materials Selection: Ensuring Reliability and Longevity
The choice of materials is essential for vacuum chamber parts. Commonly used materials include:
Stainless Steel 304/316: Offers excellent corrosion resistance and durability.
Aluminum Alloys: Lightweight and thermally conductive, suitable for specific chamber components.
Ceramics: Used in applications requiring high thermal and electrical resistance.
Titanium: Low outgassing properties make it ideal for ultra-high vacuum environments.
These materials are carefully inspected to meet industry specifications that ensure long-term reliability and operational efficiency.
4. The Manufacturing Process: Precision and Expertise
The crafting of vacuum chamber parts involves advanced manufacturing techniques:
CNC Machining: Ensures extreme precision in shaping components to tight tolerances.
Welding and Assembly: High-grade welding methods, such as TIG welding, create airtight seals critical for vacuum performance.
Surface Treatments: Electro-polishing and passivation reduce contamination risks and enhance durability.
Ultra-Cleaning Processes: Rigorous cleaning eliminates microscopic particles that could compromise vacuum integrity.
These steps demand a combination of cutting-edge technology and skilled craftsmanship.
5. Quality Control: Upholding Excellence at Every Step
Quality control is a cornerstone of semiconductor vacuum chamber part manufacturing. Stringent measures ensure that every component meets exacting standards.
Dimensional Accuracy: Precision measuring tools verify adherence to design specifications, including CMM (Coordinate Measuring Machines).
Leak Testing: Helium leak detection ensures components are airtight and suitable for high-vacuum applications.
Surface Analysis: Advanced instruments assess the smoothness and cleanliness of surfaces to prevent contamination.
Stress and Fatigue Testing: Components are tested for mechanical integrity under simulated operational conditions.
Documentation: Each part is delivered with a comprehensive quality report detailing all inspections and tests performed.
6. Certifications, Codes, and Standards
To meet global industry requirements, manufacturers must adhere to strict certifications and standards, including:
ISO 9001: Quality Management Systems certification ensuring consistent product quality.
ASME Standards: Compliance with the American Society of Mechanical Engineers' codes for pressure vessels and components.
RoHS Compliance: Ensures parts are free from hazardous substances.
SEMATECH Guidelines: Industry-specific standards for semiconductor manufacturing equipment.
CE Marking: For components exported to the European Union, indicating conformity with health, safety, and environmental protection standards.
Certifications enhance credibility and assure clients of consistent quality and compliance with international regulations.
7. Challenges Faced by Manufacturers
Producing and exporting semiconductor components comes with several challenges:
Stringent Tolerances
Semiconductor processes demand parts manufactured to micrometer-level tolerances. Achieving such precision requires advanced CNC machines and highly skilled technicians.
Contamination Control
Even microscopic contamination can compromise vacuum chambers' performance. Maintaining cleanroom conditions and employing rigorous cleaning protocols are essential but costly measures.
Global Compliance
Navigating the complex web of international certifications and export regulations requires dedicated compliance teams and ongoing process updates.
Material Sourcing
Obtaining high-quality, traceable materials is a challenge, especially during global supply chain disruptions. Manufacturers must build strong supplier relationships to ensure consistency.
Cost Efficiency
Balancing the demand for high-quality components with competitive pricing is an ongoing challenge, especially in a market with tight margins.
8. Packaging for Export: Preserving Quality in Transit
Proper packaging is crucial to protect vacuum chamber parts during transport. Our packaging process includes:
Vacuum-Sealed Wrapping: Prevents contamination by sealing components in protective layers.
Shock-Resistant Containers: Ensures components are safe from impact damage.
Moisture Protection: Desiccants and airtight packaging prevent corrosion during shipping.
Additionally, eco-friendly packaging materials are available to align with sustainability goals.
9. Exporting Process: Delivering Globally with Precision
Exporter ensure smooth and reliable delivery to clients worldwide. Key steps include:
Documentation: Providing certificates of origin, customs documentation, and detailed quality reports.
Compliance: Meeting import regulations of target countries, including CE marking for Europe and ISO certifications.
Logistics Partnerships: Collaborating with reputed shipping providers for efficient and timely delivery.
Our robust export framework ensures that every shipment arrives in perfect condition.
10. The Future of Semiconductor Vacuum Chamber Parts Manufacturing
The future of semiconductor parts manufacturing is driven by innovation and sustainability. Advancements include:
Additive Manufacturing (3D Printing): Enabling rapid prototyping and production of complex components.
Advanced Coatings: Developing low-outgassing and self-cleaning coatings to enhance performance.
Sustainable Manufacturing: Reducing environmental impact through energy-efficient processes and recyclable materials.
By staying ahead of these trends, manufacturers can continue to meet the evolving needs of the semiconductor industry.
Conclusion: Crafting Excellence for the Semiconductor Industry
Manufacturing and exporting chamber vacuum parts is a complex process that demands precision, quality, and compliance with global standards. From material selection and rigorous quality control to overcoming industry challenges, every step reflects a commitment to excellence.
Commentaires