Tolerances in Aluminum Machining Parts: What You Need to Know
- synergypepg
- Nov 13, 2024
- 3 min read
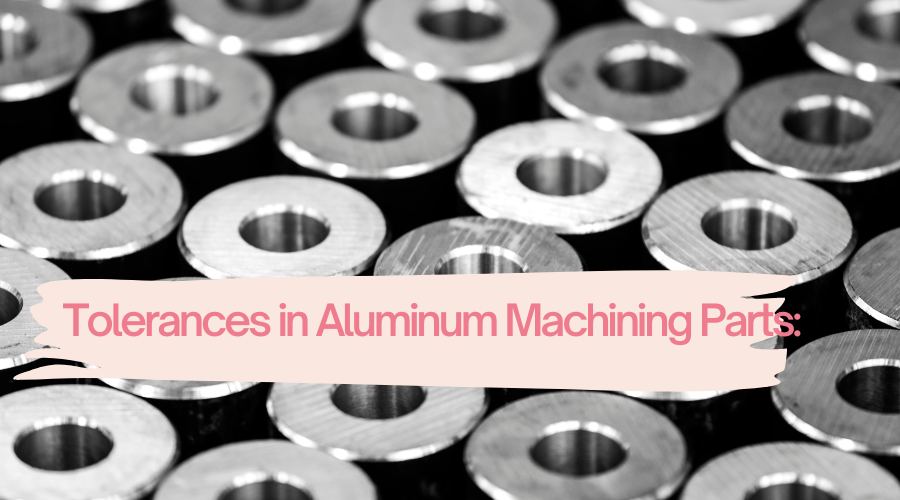
Tolerances are the allowable variations in a part's dimensions, which ensure that each piece fits and functions as intended. For industries that rely on precision, such as aerospace, automotive, and electronics, tolerances in wholesale aluminum machining parts are vital to maintaining quality, performance, and reliability. This guide covers everything you need to know about tolerances in aluminum machining, from why they matter to how they're achieved and what factors influence them.
What Are Tolerances in Machining?
Tolerances in machining refer to the allowable deviation from specified dimensions. Every part has specific dimensions, but achieving the exact size and shape can be challenging due to material properties, machining techniques, and environmental factors. By establishing tolerances, manufacturers ensure that each part falls within a range of acceptable sizes, allowing for precise assembly and optimal performance.
Types of Tolerances in Machining
There are several types of tolerances to consider in aluminum machining, including:
Dimensional Tolerances define the acceptable range for a part's dimensions, such as length, width, or diameter.
Geometric Tolerances focus on the part's shape and form, ensuring that angles, flatness, and other features meet specific standards.
Surface Tolerances: Surface tolerance refers to the smoothness or roughness of the part's surface, which can impact its fit, functionality, and aesthetic appeal.
Each type of tolerance plays a unique role in ensuring that the final part is suitable for its intended application.
Commonly Used Tolerances for Aluminum Parts
In aluminum machining, tolerances vary depending on the part's function and the industry's requirements. However, some general guidelines apply. For precision aluminum machining, tolerances are typically between ±0.001" to ±0.005". However, parts requiring extreme precision, such as those used in aerospace, might demand tolerances as tight as ±0.0001". Understanding these general tolerances helps in planning machining processes and setting realistic expectations.
Factors That Influence Tolerances in Aluminum Machining
Several factors can impact the tolerances achievable in aluminum machining, including:
Material Properties: Aluminum's softness and high thermal conductivity can cause expansion or contraction, impacting precision.
Machining Process: Different techniques (like CNC milling or turning) provide varying levels of accuracy and finish.
Tooling Quality: Worn or low-quality tools can result in inconsistent tolerances.
Environmental Conditions: Temperature and humidity changes in the machining environment can affect aluminum's stability, potentially impacting tolerance levels.
Machine Calibration: Regularly calibrating machinery ensures it operates within desired tolerance levels.
Machining Techniques to Achieve Tight Tolerances in Aluminum
Precision machining for aluminum parts requires techniques that allow for tight tolerances. Common methods include:
CNC Machining: CNC machines offer high precision, allowing for extremely tight tolerances. By automating the process, CNC machining minimizes human error, which is crucial for maintaining consistency across large production runs.
Electrical Discharge Machining (EDM): Although less common for aluminum, EDM can achieve extremely high precision and is often used when intricate details are needed.
High-Speed Machining (HSM): High-speed machining allows for fine finishes and reduced thermal distortion, which help achieve tighter tolerances.
Choosing the right machining technique is critical to maintaining high-quality tolerances for aluminum parts.
Tools and Technology for Measuring Tolerances
Measuring tools and technologies are vital in ensuring that parts meet specified tolerances. Some commonly used tools in aluminum machining include:
Coordinate Measuring Machines (CMM) measure the exact dimensions of a part by probing various points and comparing them to the design specifications.
Micrometers and Calipers: While less advanced, these tools are still widely used for quick and accurate measurements.
Laser Scanners: Laser technology offers high precision and is effective for complex parts with intricate shapes.
Using the correct measurement tools is crucial to maintaining quality control and verifying that tolerances are met consistently.
The Cost Implications of Tight Tolerances
Achieving tighter tolerances often requires specialized tools, advanced techniques, and meticulous quality control, which can increase production costs. However, it is essential to balance costs with the necessary precision. For example, parts with more lenient tolerances may be less costly to produce but may not perform as well in demanding applications. Manufacturers and clients must communicate to establish realistic tolerances that meet performance requirements without driving up costs unnecessarily.
Tips for Achieving Tolerances in Aluminum Machining
Here are some best practices for maintaining consistent tolerances in aluminum machining:
Use High-Quality Cutting Tools: Investing in quality tools reduces the likelihood of variations in tolerance levels.
Maintain Machine Calibration: Regularly calibrate machines to prevent errors caused by misalignment or wear.
Monitor Environmental Conditions: Maintain stable temperature and humidity levels to minimize the effects of thermal expansion.
Conduct Regular Inspections: Periodic inspections ensure that parts consistently meet tolerance requirements.
Conclusion
Tolerances in aluminum machining ensure that parts meet precise specifications and function as intended. From understanding different types of tolerances to choosing appropriate machining techniques and monitoring environmental factors, several factors contribute to achieving optimal tolerance levels. By focusing on quality control, consistent monitoring, and choosing the right tools, manufacturers can produce aluminum parts that meet the strict requirements of high-precision applications. In industries where performance and reliability are critical, understanding and achieving the correct tolerances is essential for success.
Comments